BPC vs WPC – Which One to Choose for Manufacturing Applications?
- Admin
- May 22, 2024
- 4 min read
Updated: Aug 6, 2024
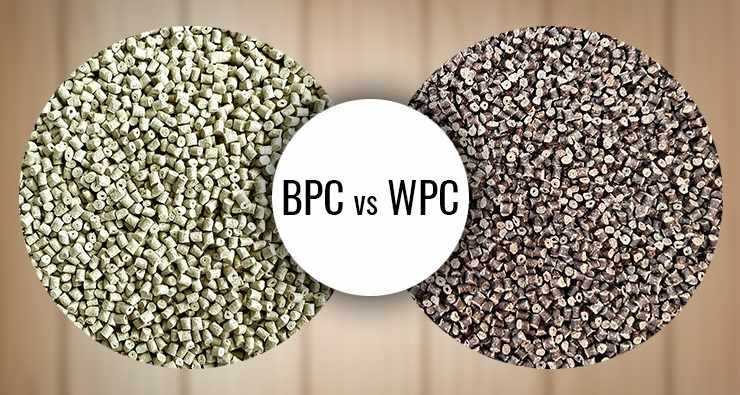
The world of manufacturing plastic products is seeing a shift in perspective. The focus is shifting onto sustainable alternatives. Manufacturers are increasingly looking to lower their carbon footprint and reduce plastic usage by replacing it with sustainable materials. There are several options that are available. The two most commonly available materials are Wood Plastic plastic (WPC) and Bamboo Plastic Composite (BPC).
Both of these materials offer an environment friendly choice for a variety of manufacturing applications.
But, have you ever thought about the difference between WPC and BPC? Which among them is best suited for various manufacturing applications?
What is BPC?
BPC stands for Bamboo Plastic Composite. As the name itself indicates, it is a biocomposite of bamboo and polymer. Bamboo is moisture proof and bamboo fibers reinforce the polymer adding stiffness to the material. As bamboo fibers have a similar appearance to wood, the end products end up being aesthetically pleasing.
BPC tends to ensure a tilt towards a greener and more sustainable future ahead. The environmental benefits include reduced dependence on non-renewable energy, low emissions and enhanced energy recovery. It also ensures a circular economy as the bamboo fibers are sourced from the waste of handicraft industry.
Various industries have adopted BPC to manufacture flower pots, pet bowls, homeware products, and construction materials like decking and cladding. Consumers in today’s time are increasingly turning towards being more environment friendly, BPC helps them to make this shift easier.
A few salient features of BPC are:
Offers High Dimensional Stability: It works well in high and low environments making it ideal for locations where weather fluctuates between extreme ends.
Aesthetic Solution: BPC is a lightweight, durable and aesthetic alternative to traditional plastic.It can be manufactured in colours according to customers needs which also eliminates the need to paint.
Mechanical Properties: BPC comes with strong mechanical properties like being slip resistant, non-toxic and scratch resistant.
BPC is widely used in:
Construction: Decking, fencing, railings, cladding, window and door profiles.
Furniture: Outdoor furniture, bathroom cabinets, kitchen countertops.
Automotive: Interior trims, dashboards, door panels.
Homeware: cutlery, crockery, tubs, baskets, storage solutions.
What is WPC?
WPC stands for Wood Plastic Composite. It is a biocomposite that is obtained by combining wood fibers and polymer. This composite gives rise to a manufacturing solution that is versatile, durable, and environmentally friendly. It not only is an alternative for traditional plastic but also conventional wood products.
WPC is a sustainable option as it helps in reducing dependence on traditional wood and plastic. The wood is sourced from the waste of the handicraft and furniture industry. This would be traditionally burnt as fuel. Thus, WPC helps in decreasing carbon footprint and environmental pollution.
The material is used for a wide range of application areas which includes decking, fencing, indoor and outdoor furniture, and a lot more. In fact, you can use it for manufacturing any product that uses plastic. Its excellent mechanical properties are the main reason behind the versatility of WPC.
Key features of WPC can be counted as:
High Resistance to Natural Elements: Products manufactured with WPC are known to have a high resistance to moisture, termites, and extreme weather conditions.
Aesthetically Pleasing: WPC helps to bring the aesthetic value of wood to plastic products, making them more attractive to the consumer. the manufacturing material.
Non-Toxic: Made from the natural elements, WPC is an excellent choice for various manufacturing applications that require it to be non-toxic and safe for use by children.
WPC finds an optimum use in:
Building and Construction: Decking, fencing, railings, window and door frames.
Interior Design: Wall panelling, furniture components, moulding, flooring
Consumer Goods: .toys, kitchenware, storage solutions.
How to Choose Between WPC & BPC?
The material you choose for your manufacturing process depends on various factors.
Some of these factors can include:
Mechanical Properties: Every manufacturing process requires different properties in terms of strength, flexibility, and ease of shaping..
Manufacturing Process: Whether your product is injection moulded, extruded or blow moulded affects the grade of BPC and WPC granules.
Aesthetic Appeals: Both BPC and WPC tick the box from this perspective. However, the choice between the two can be influenced by the custom needs of the manufacturer in terms of visibility of fiber and colour.
End use and performance: This is one of the important factors when it comes to making the right choice between WPC and BPC.
Conclusion
Both WPC and BPC are best suited for multiple manufacturing applications. In the realm of the sustainable manufacturing industry, each of these materials comes with a plethora of advantages. Having a good knowledge of each of these materials and the specific needs you may have will help you make an informed decision in picking the best among them.
RRAJ Bioplast is the leader in pioneering sustainable alternatives to plastic. At RRAJ Bioplast we do not want to be just a product company, we want to be a narrative builder to define how sustainability can be spoken of in a meaningful way. Our vision is to transform waste into usable end-products that converts it into a long-term solution for the system.
We provide support with material selection & new material development. We take pride in supporting product manufacturers to make their products sustainable and more environment friendly. We can customize colour, fiber choice (bamboo, wood), fiber visibility (high, medium, low), MFI & mechanical properties as per your product’s needs. We can also manufacture biodegradable biocomposites on demand of the manufacturers.
Contact Us:
Phone: +91-9310026933, +91-9311026933
Email: info@rajbioplast.com
댓글